What to expect when you are expecting a field label evaluation
You’ve just setup and installed your new custom machine in your facility…
and the custom machine is powered on and ready for production. It’s in its final install location. You’ve securely anchored it with seismic bracing because it is over 400lbs, and well, it’s just a good thing to do in general because you value employee safety. Your general contractor is going through the final checklist of items needing verification for building permit sign-off ahead of the city inspector’s final visit to your newly built facility.
The day of the final inspection arrives and everything is looking good. That is, until the city’s electrical inspector takes a look at your custom machine. He can’t find a visible nameplate on the outside and he can’t locate any field evaluation body (FEB) sticker or NRTL marking to confirm the machine is listed. The inspector hands you a list of recognized FEBs and NRTLs and informs you that until the machine has had a field label evaluation and has been verified to be electrically compliant with the local AHJ‘s interpretation of NFPA codes concerning electrical safety, he cannot sign off on your building permit.
You’re now stuck. You weren’t expecting a field label evaluation and now you’re desperately in need of one to begin production at your facility.
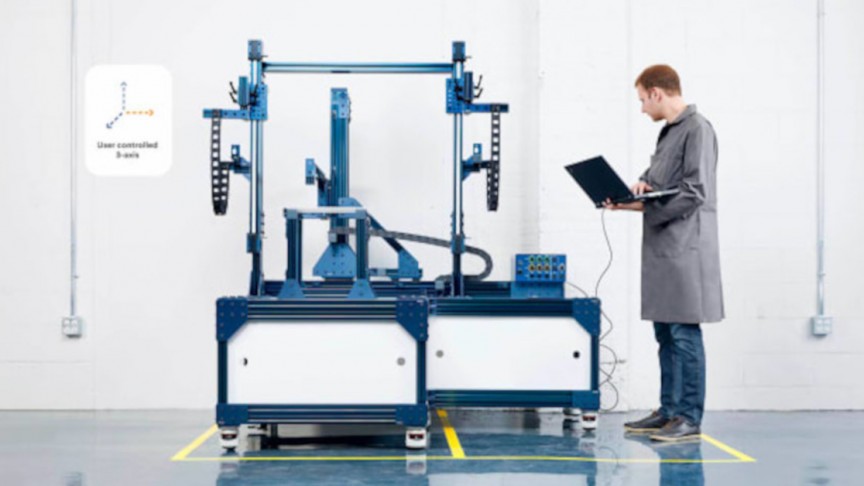
So, what should you expect when you are expecting a field label evaluation?
Documentation is key
A FEB or an NRTL will request as much supporting material as possible about the machine needing a 3rd party electrical evaluation (also known as a field label or a field evaluation).
This can include the machine’s manual (this may not apply if this is a custom tool) and any other available documentation including schematics, facility layout, and a BOM (Bill of Materials) for the machine.
Once all available supporting documentation for the unlisted machine is forwarded on, a proposal for services can be generated for review and work-start.
The machine must be in safe operating condition
Upon acceptance of a proposal for services an FEB like Lewis Bass will want to coordinate with your facility manager/director to confirm the machine is in a safe, working state prior to an engineer visiting the facility.
Additionally, many of the electrical tests being performed on the machine to evaluate compliance require full-load and a machine operator to be present to open the electrical panels and cycle the machine.
EMO (emergency off buttons), shielding on machines with moving parts, and properly routed/protected wiring should all be verified to be in proper functional order prior to the engineers visit.
If non-compliances are found in the machine
When an engineer performs the evaluation on the machine he/she may make note of certain non-compliances that may disqualify the machine from being successfully evaluated/passed and labeled for use.
In situations where areas of a machine’s non-compliance are of a physical nature and require re-engineering to become compliant, recommendations will be passed along and are expected to be addressed prior to the engineer re-evaluating the machine for electrical compliance.
Lewis Bass refers to this pre-evaluation list of non-compliances as a punch-list and can refer clients to our trusted partners for mitigations.
A final electrical evaluation is performed and the machine is labeled
Once the punch-list (if required) is completed and the machine is deemed to be in a compliant state for evaluation, an engineer will proceed down a checklist of electrical and visual tests to ensure the machine is safely operating within acceptable electrical parameters.
Once every test is performed a label will be affixed to the machine with a corresponding number that will match up to a report generate for the customer and the AHJ/local city.
The machine can now be safely operated and put into production—-which means good news for your building permit, too. It can now fully signed off.
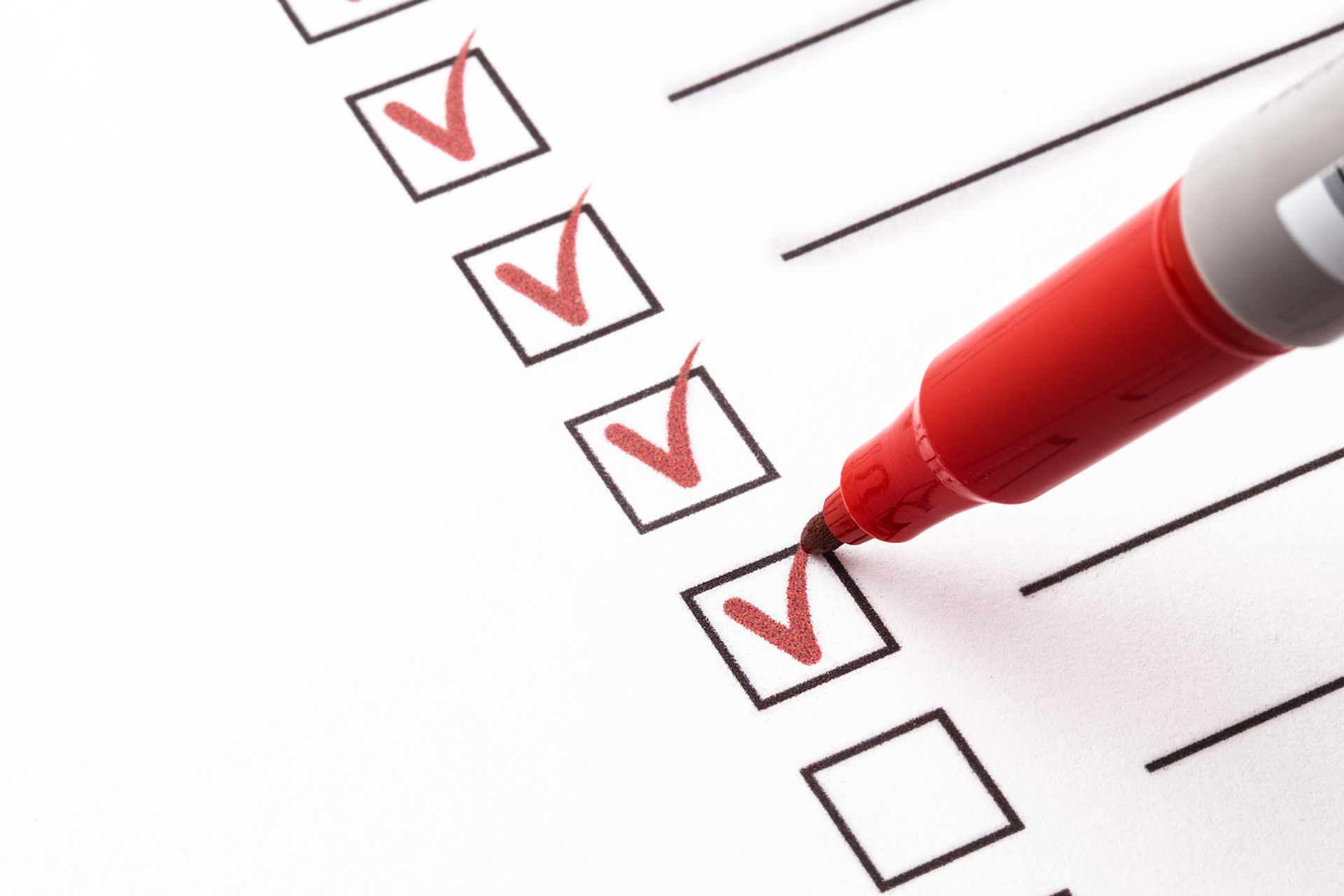
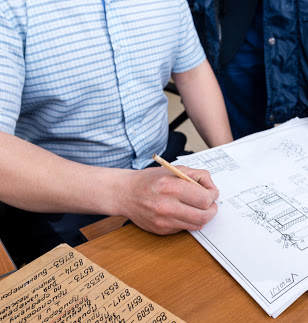
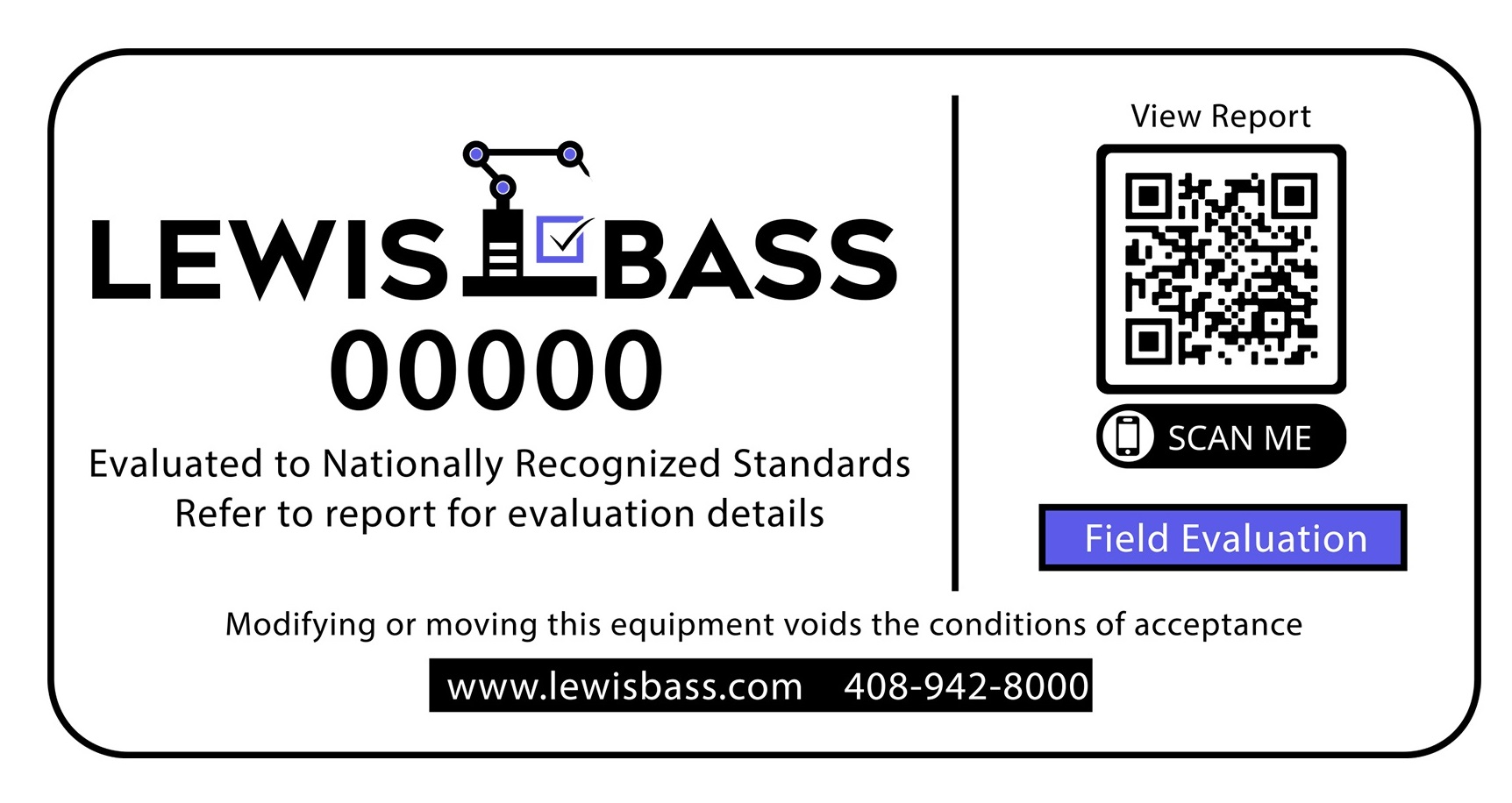
Do you have a need for our services?
Lewis Bass can help your team identify the most common safety issues in your facility, along with providing immediate referrals to our trusted partners to address them on your behalf.
Not sure what service you need from us?
Take our service identifier quiz here.
Are you uncertain if your equipment is unlisted or not at your facility?
Lewis Bass has you covered here as well: download our unlisted equipment self-identification flyer here.
Do you have a need for an urgent machinery evaluation?
Please reach out to us using our contact form here or call us directly at our office line 408-942-8000. We are always available to help with rush jobs and permit-blocking safety situations at your facility.