What is an Authority Having Jurisdiction (AHJ) and why should you care?
What is an Authority Having Jurisdiction?
In North America, an AHJ (Authority Having Jurisdiction) acts as the enforcement arm of the NFPA 79/790/791 codes that govern our industry when it comes to electrical evaluations of equipment.
While it was not intended to be confusing, the fact of the matter is that the AHJ isn’t just one person or office.
For instance, for a fire safety issue, the AHJ may be a fire marshal. For a structural issue, the AHJ may be a building code inspector. For a health or public safety issue, it may be an emergency management agency director or health department.
For engineering contractors dealing with electrical evaluations of equipment the AHJ representative is an electrical inspector.
It is important to note that no single AHJ is the same in its approach and requirements and that often times, when a building permit is being verified for sign-off, an AHJ’s authority is often left in the hands of a single inspector in the field who may require certain actions be performed for verifying the safety of your electrical machinery based on his/her read of the situation.
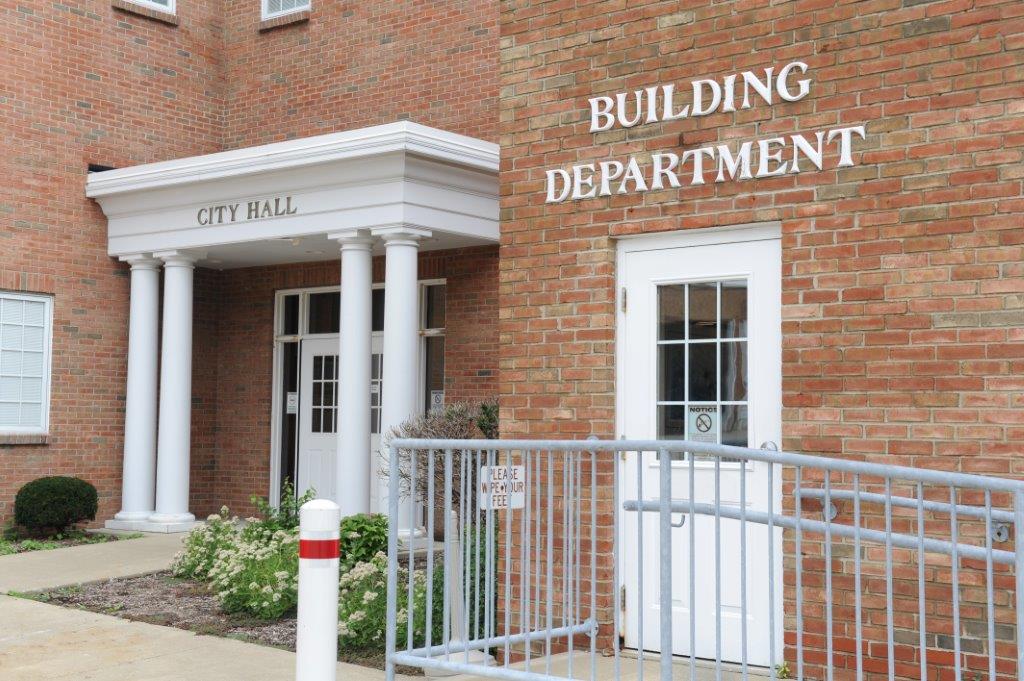
AHJs come in many forms
Typically, an AHJ is located within your city’s governmental structure. However, in certain situations it can also be for an entire county like LA County, US army bases, or even the DOE (Department of Energy) itself.
NFPA codes classify the Authority Having Jurisdiction as “an organization, office, or individual responsible for enforcing the requirements of a code or standard, or for approving equipment, materials, an installation, or a procedure.”
In the annex of codes, this definition is further added to:
“Where public safety is primary, the AHJ may be a federal, state, local, or other regional department or individual such as a fire chief; fire marshal; chief of a fire prevention bureau, labor department, or health department; building official; electrical inspector; or others having statutory authority. For insurance purposes, an insurance inspection department, rating bureau, or other insurance company representative may be the AHJ.”
This statement reinforces the fact that the AHJ is typically far more than just an individual entity. Instead, it is viewed as a collective force of representatives from a local government. The AHJ could work for the state or a federal agency, in some cases they come from the private sector, for instance when it comes to insurance.*
*Source: https://www.highlandwireless.com/ahj-what-is-it-and-what-does-it-mean-for-your-business/
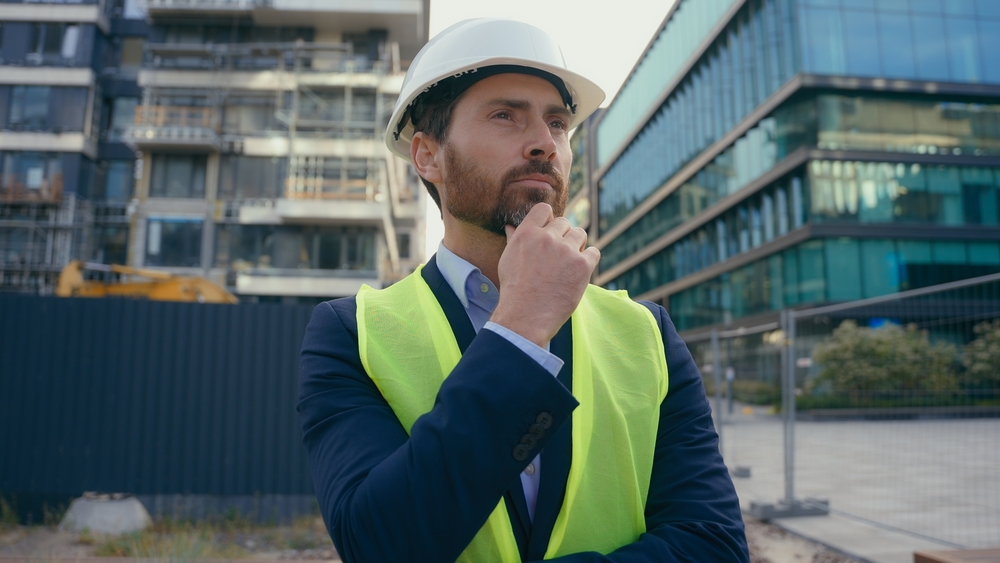
Lewis Bass does its work on behalf of AHJs
While companies like Lewis Bass are the ones doing the work to get your machinery compliant and safe, what is not commonly known is that an Authority Having Jurisdiction is the primary driving force behind requiring the work to be performed in the first place.
Lewis Bass (referred to as FEB or Field Evaluation Body) is called in by companies that have been given feedback from city inspectors/AHJs during their final building permit sign-off that certain unlisted electrical equipment needs to be 3rd party certified.
A key part of this symbiotic relationship between AHJs and 3rd party inspectors that establishes this link of accountability is the requirement of reports and sticker logs.
Reports from the 3rd party inspector must fully explain the results of the electrical safety testing performed on the equipment and the testing equipment must have been recently calibrated. Additionally, the report submitted to the AHJ must correspond to a unique sticker number affixed to each machine that has passed evaluations.
When a 3rd party inspector (FEB or NRTL) comes to the facility to perform the evaluations of the equipment it is in fact at the request of the AHJ itself even though the company pays the inspector for the service.
The only difference is the timing for when the 3rd party inspector is called out to perform the required work.
Two common situations can apply:
1) When the AHJ requests it for equipment, the company must reach out to approved inspectors for that city and schedule the evaluations to be performed.
2) The company itself is aware of the equipment being non-listed, custom manufactured, or has previously had evaluations performed and is moving facilities and seeks out a 3rd party inspector earlier on in the process to avoid permit delays.
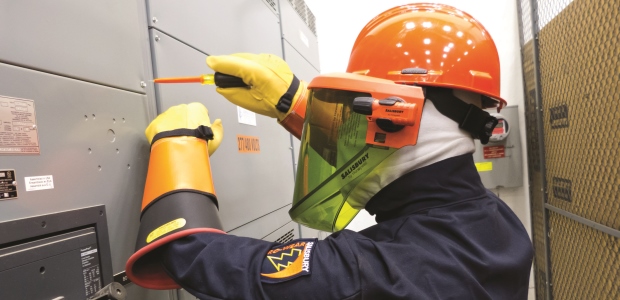
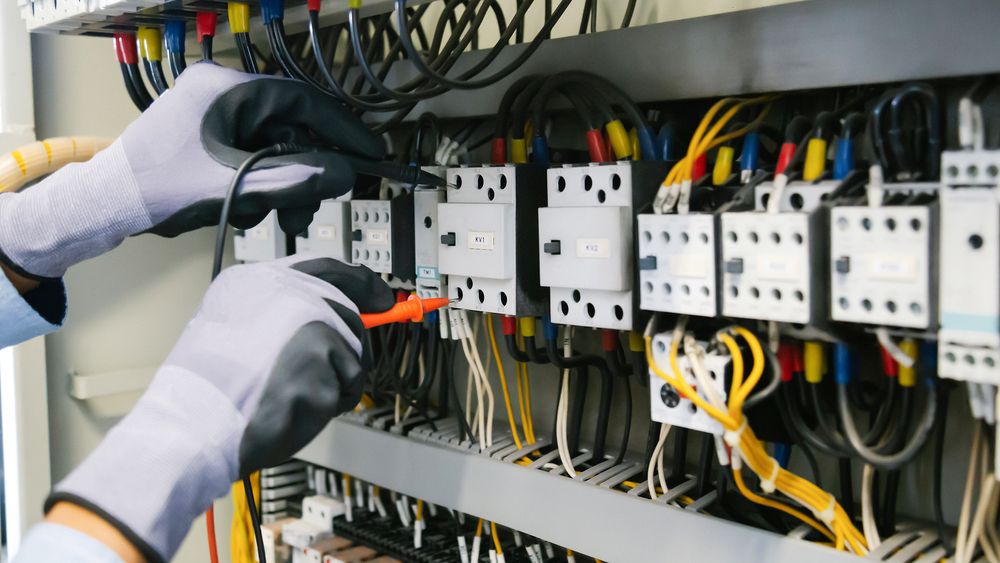
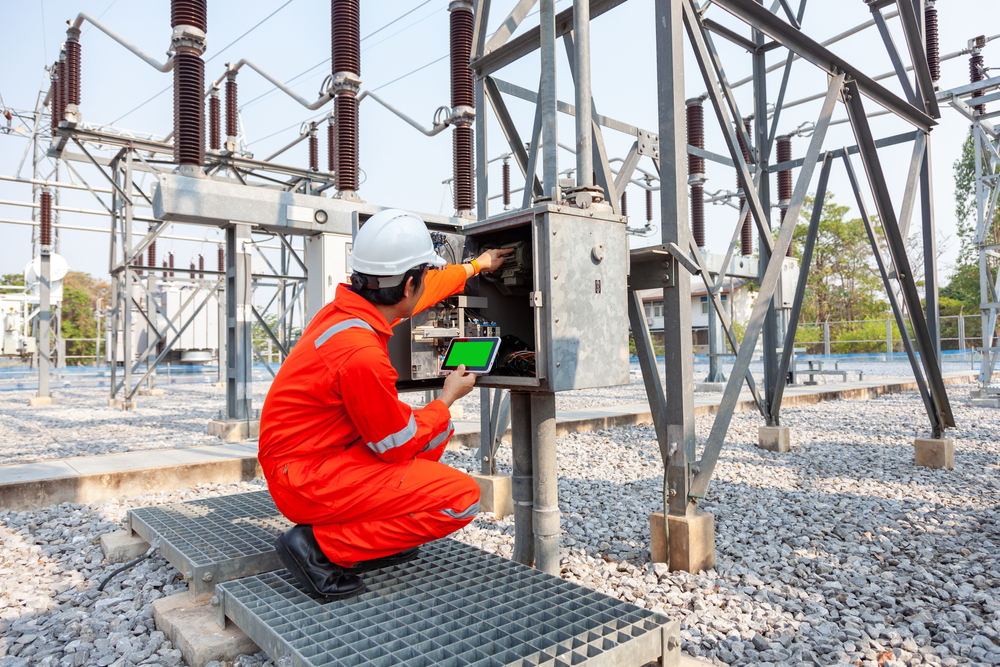
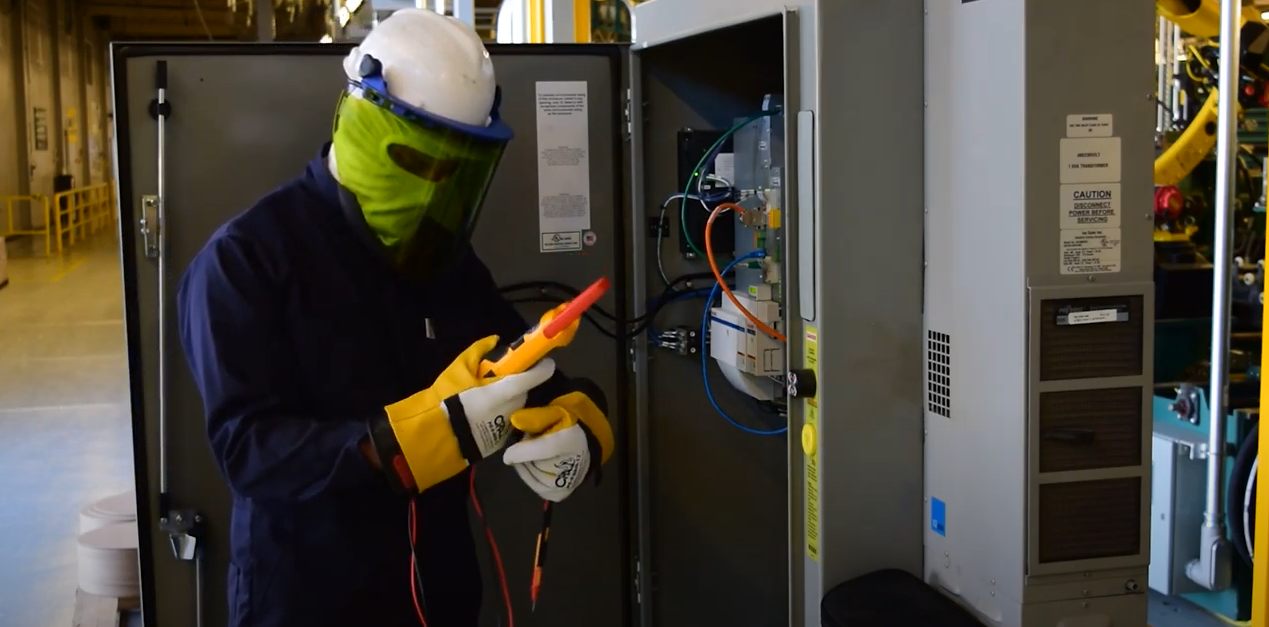
Strategies for Dealing with Your Local Authority Having Jurisdiction
Navigating the intricacies of your local Authority Having Jurisdiction (AHJ) can be a daunting task, but with the right strategies, you can ensure your electrical equipment meets all necessary requirements and achieve a smooth permit sign-off process. Here are some key approaches to keep in mind:
Early Engagement and Communication
One of the most effective strategies is to engage with your AHJ early in the project. Schedule a preliminary meeting to discuss your project plans and get a clear understanding of the specific requirements and standards they enforce. This proactive approach can help identify potential issues before they become major roadblocks.
Thorough Documentation
Ensure all your documentation is thorough and up-to-date. This includes detailed plans, specifications, and any necessary calculations. Having a well-organized and comprehensive documentation package can significantly streamline the review process and demonstrate your commitment to compliance.
Leverage Expertise
Consulting with experts who have experience dealing with local AHJs can be invaluable. These professionals can provide insights into common pitfalls and effective strategies for navigating the approval process. Consider hiring a consultant or a project manager who specializes in compliance with local regulations.
Stay Informed on Code Changes
Building codes and standards are frequently updated. Staying informed about these changes is crucial. Regularly check for updates from relevant regulatory bodies and ensure your project aligns with the latest codes. This can prevent last-minute surprises and rework.
Build Relationships
Building a positive relationship with your AHJ can go a long way. Be respectful and cooperative in all your interactions. Establishing a good rapport can lead to smoother communication and a more collaborative approach to addressing any issues that arise.
It is also helpful to solicit advice and schedule facility walk-throughs with electrical and facility safety specialists to generate a list of potential blockers and steps to address them prior to a city inspection.
Be overly prepared for an inspection
As one cannot predict the exact requirements and legal interpretations that any specific AHJ may use in your area, it is important to be overly prepared prior to their visiting for permit sign-off. This is doubly-true if you are installing new equipment or moving facilities (and equipment) to a new AHJ you are not familiar with.
Inspections are a critical part of the approval process. Make sure your project site is well-prepared for these visits. Conduct internal inspections and address any issues beforehand. Being ready for an inspection demonstrates professionalism and can expedite the approval process.
What Are Some Common Last-Minute Project Blockers?
- Incomplete Documentation: Missing or incomplete documentation is a common cause of delays. Ensure all necessary paperwork is complete and easily accessible.
- Non-Compliance with Updated Codes: Projects sometimes overlook recent code changes. Regularly verify that your project complies with the latest standards.
- Unresolved Safety Concerns: Safety is a top priority for an Authority Having Jurisdiction (AHJ). To ensure permit sign-off, you should check and correct equipment safety non-compliances from both a worker safety standpoint (shielding, EMO buttons, safety signs, etc) and also from an electrically operational one: is the equipment NRTL listed or evaluated by an FEB?
- Unclear Communication: Miscommunication between project stakeholders and the AHJ can lead to misunderstandings and delays. Maintain clear and consistent communication throughout the project.
Do you have a need for our services?
Lewis Bass can help your team identify the most common safety issues in your facility, along with providing immediate referrals to our trusted partners to address them on your behalf.
Not sure what service you need from us?
Take our service identifier quiz here.
Are you uncertain if your equipment is unlisted or not at your facility?
Lewis Bass has you covered here as well: download our unlisted equipment self-identification flyer here.
Do you have a need for an urgent machinery evaluation?
Please reach out to us using our contact form here or call us directly at our office line 408-942-8000. We are always available to help with rush jobs and permit-blocking safety situations at your facility.