The Top 10 Safety Checks Every Facility Should Conduct Annually
When it comes to running a safe and efficient facility, there’s no room for shortcuts.
Regular safety checks are a facility’s first line of defense, keeping both employees and equipment secure while ensuring that operations run smoothly. But with so many aspects of facility management to consider, how do you prioritize your annual safety checks?
Whether you’re overseeing a small manufacturing plant or a sprawling industrial complex, here are the top 10 safety checks every facility should conduct annually. By making these checks a regular part of your maintenance calendar, you’re not only meeting compliance standards but also establishing a proactive culture of safety that benefits everyone.
1.) Fire Safety Equipment and Protocols
First on our list of top 10 safety checks is fire safety. Fire hazards can be devastating, making it crucial to have all equipment in top shape. This means inspecting fire extinguishers, ensuring they’re accessible and charged, and checking fire alarm systems and sprinklers. Look into fire evacuation protocols as well, confirming that every team member understands the process and that exit paths are well-marked and free of obstacles. Fire safety is one area where proactive checks truly save lives and prevent costly damages.
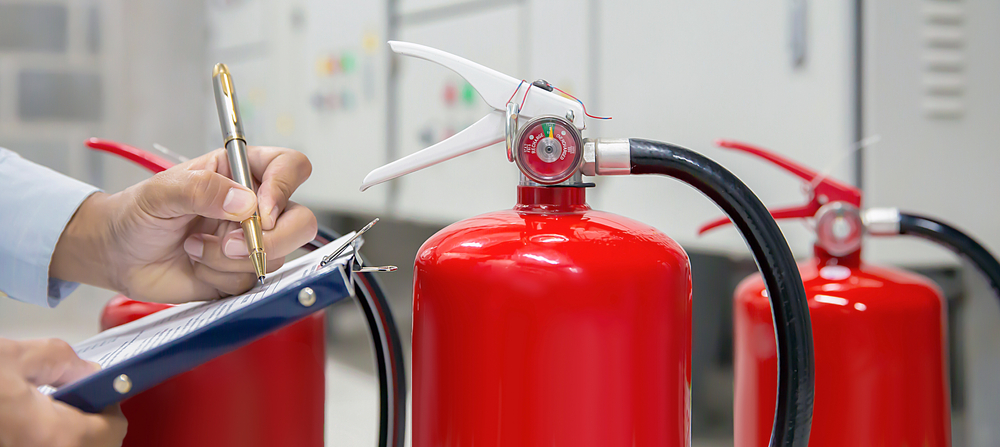
2.) Electrical Systems and Wiring Inspections
Aging electrical systems and faulty wiring are significant safety hazards in any facility. Schedule a thorough inspection of your facility’s electrical systems, focusing on circuit breakers, panels, and grounding. Check for any exposed or worn-out wiring that could lead to a potential fire hazard. Electrical safety should be taken seriously to prevent fires, equipment failure, or even electrocution risks. A qualified electrician should conduct these checks annually to ensure everything is in compliance with the latest safety codes.
Lewis Bass takes this safety check seriously and incorporates this guidance directly into our field evaluation service for unlisted equipment as mandated by NFPA 791.
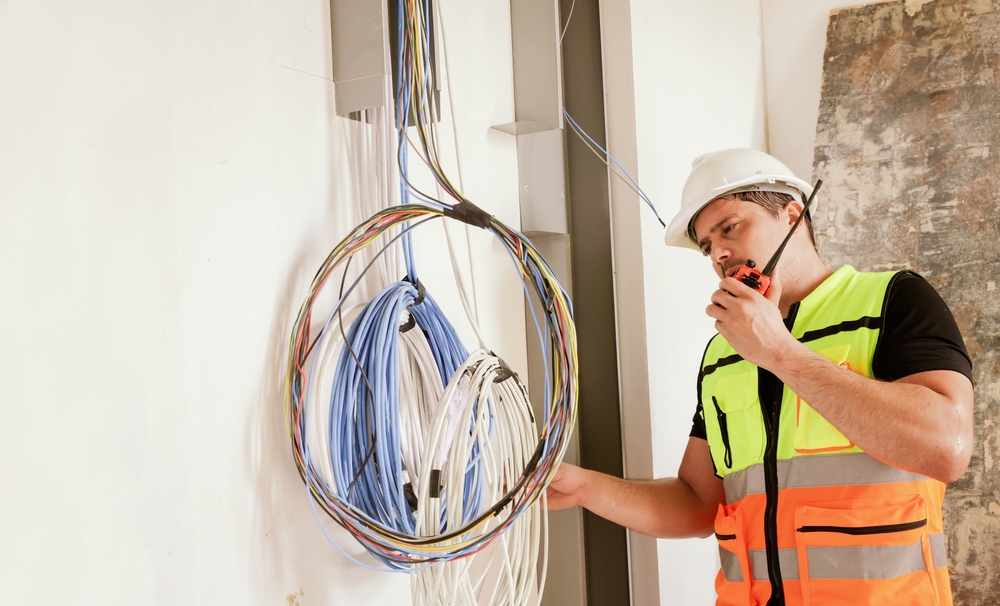
3.) Emergency Exits and Evacuation Plans
Emergency exits are lifesavers in crisis situations, and they need to be maintained accordingly. Ensure all exit doors function without obstruction and that escape routes are clear, marked, and free from any stored items. Emergency lighting should also be tested to guarantee visibility in a power outage. Additionally, update and review evacuation plans with your team, particularly if there have been changes in facility layout. This check will prepare your team for a quick and safe exit in any emergency.
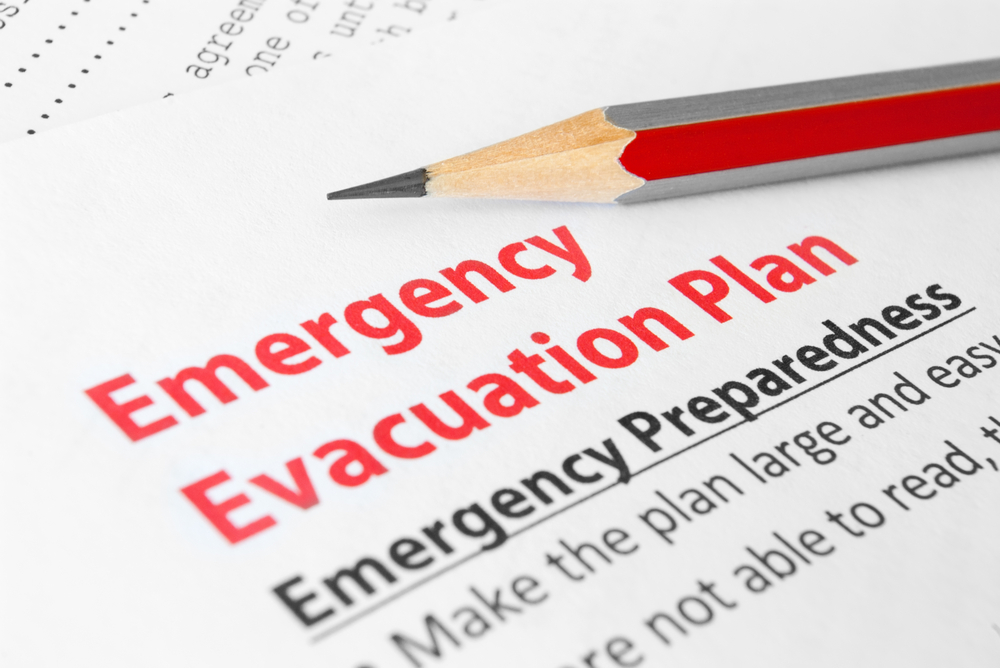
4.) Machinery and Equipment Maintenance
Routine machinery checks reduce the risk of unexpected breakdowns and enhance safety. An annual inspection should cover lubrication, alignment, and general maintenance of all major equipment. Assess guards and protective devices to confirm they’re secure and in working order. Don’t forget to review the manufacturer’s maintenance guidelines as well; they provide specific insights on extending the lifespan and safety of the equipment. With regular machinery inspections, you’re minimizing the likelihood of injuries caused by faulty or poorly maintained equipment.
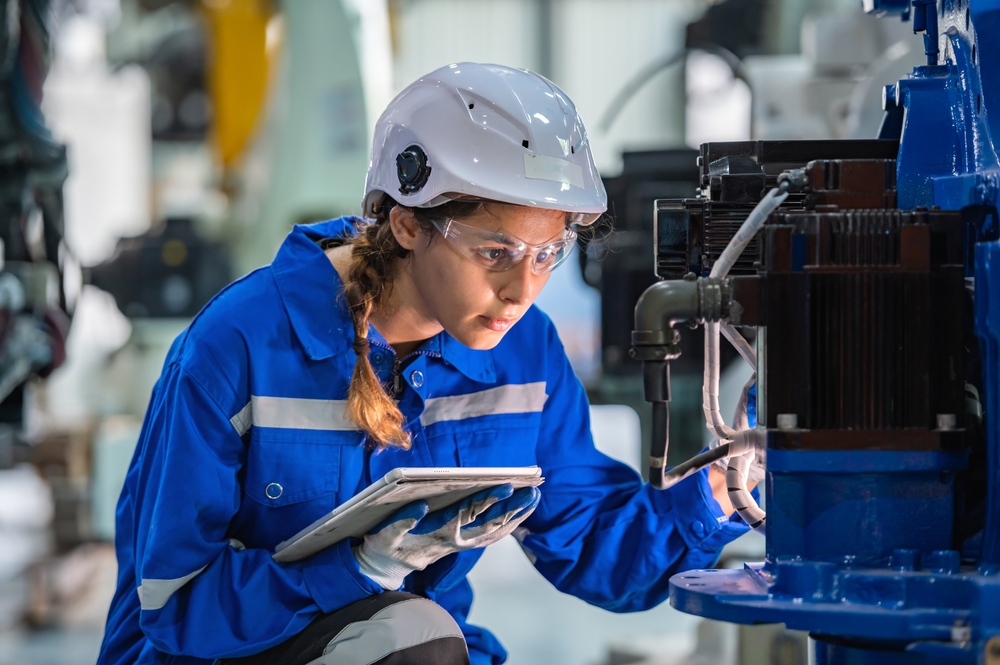
5.) Personal Protective Equipment (PPE) Evaluation
Personal Protective Equipment (PPE) is only as effective as it is available and correctly used. Conduct an annual review of PPE availability and assess its condition. Replace any damaged or outdated items, and ensure all employees have access to the PPE they need. This check should also include PPE training refreshers, as employees need to know the correct way to use protective gear. A well-maintained stock of PPE minimizes risks and is a requirement for a safe working environment.
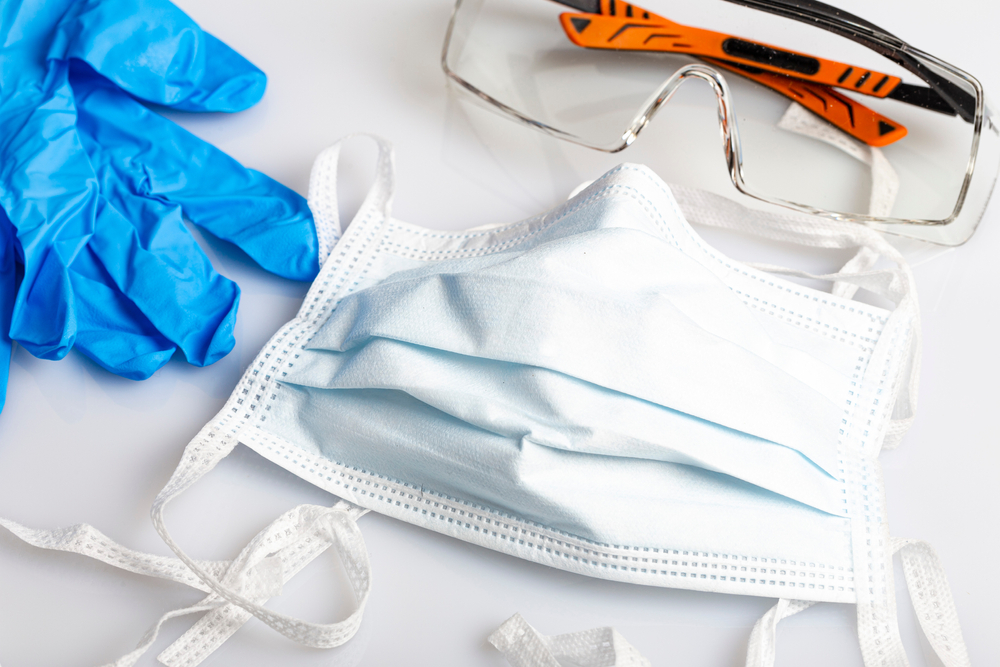
6.) HVAC Systems and Indoor Air Quality
A facility’s HVAC system isn’t just about comfort; it plays a crucial role in maintaining air quality and reducing the risk of airborne contaminants. Check that ventilation systems are clean and functioning effectively, and replace filters if needed. Assess humidity and temperature controls to prevent mold and other air quality issues. Annual HVAC checks not only maintain employee comfort but also prevent health issues caused by poor air quality.
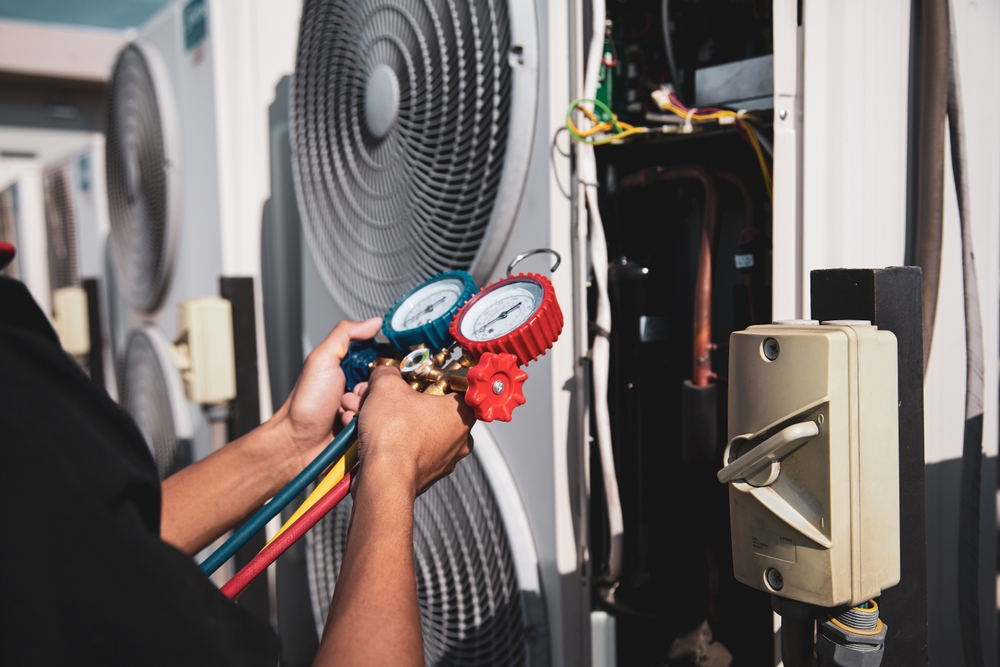
7.) Hazardous Material Storage and Handling
Facilities that handle hazardous materials require stringent controls for storage, handling, and disposal. Ensure all hazardous substances are stored in compliance with local and federal regulations, and that containers are properly labeled. Review storage practices, check for leaks, and confirm that employees are trained in handling procedures. Additionally, ensure spill containment systems are readily available and functional. Properly handling hazardous materials keeps both employees and the environment safe.
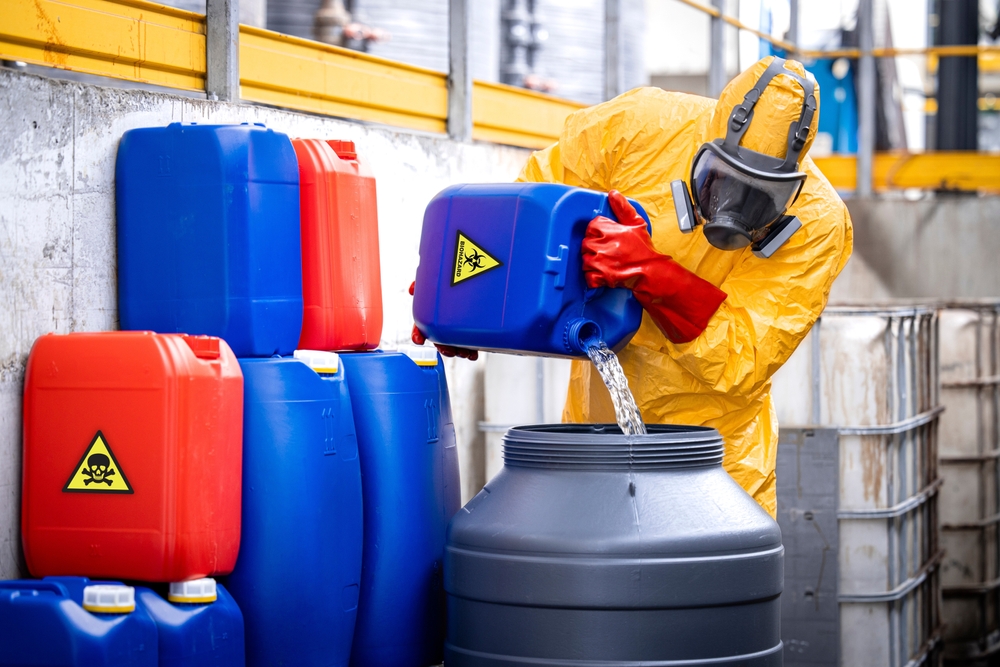
8.) Safety Signage and Labeling
Clear, visible safety signage is essential for guiding employees, especially in emergency situations. During your annual review, check that all safety signs are properly placed, visible, and compliant with regulatory standards. Labels on machinery, hazardous materials, and PPE areas should be clear and up-to-date. This simple yet crucial safety check ensures everyone on site knows what’s expected in various areas and understands potential hazards.
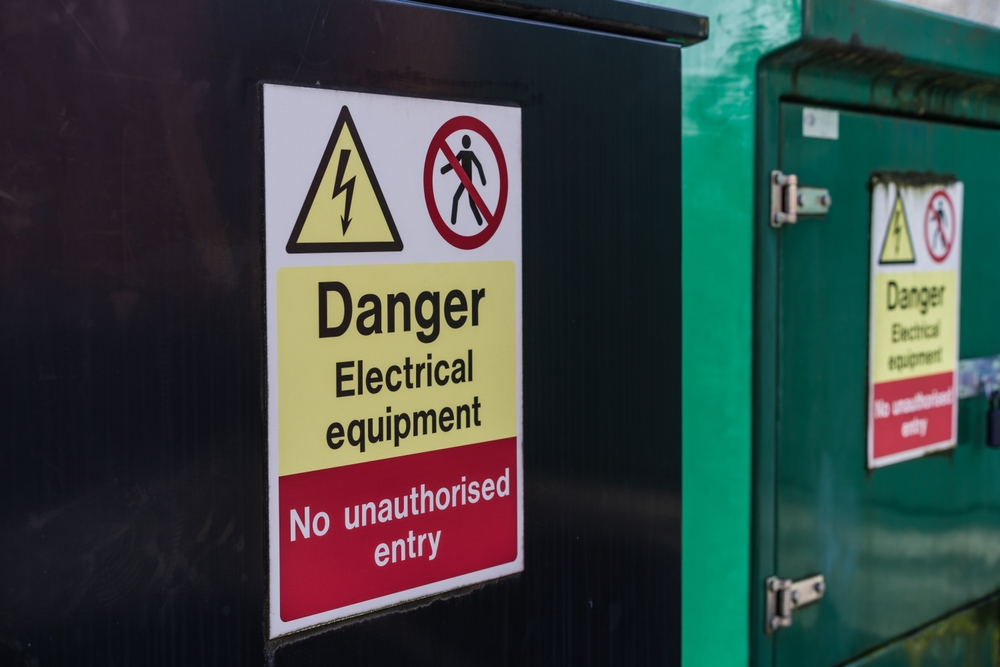
9.) First Aid Stations and Medical Supplies
In any workplace, quick access to first aid can make a significant difference during emergencies. Ensure that all first aid stations are fully stocked, and check expiration dates on supplies like antiseptics, bandages, and medications. It’s also wise to keep an eye on supplies that get used frequently and may need restocking more than once a year. Providing adequate medical supplies contributes to an immediate response to injuries, minimizing the potential for long-term damage.
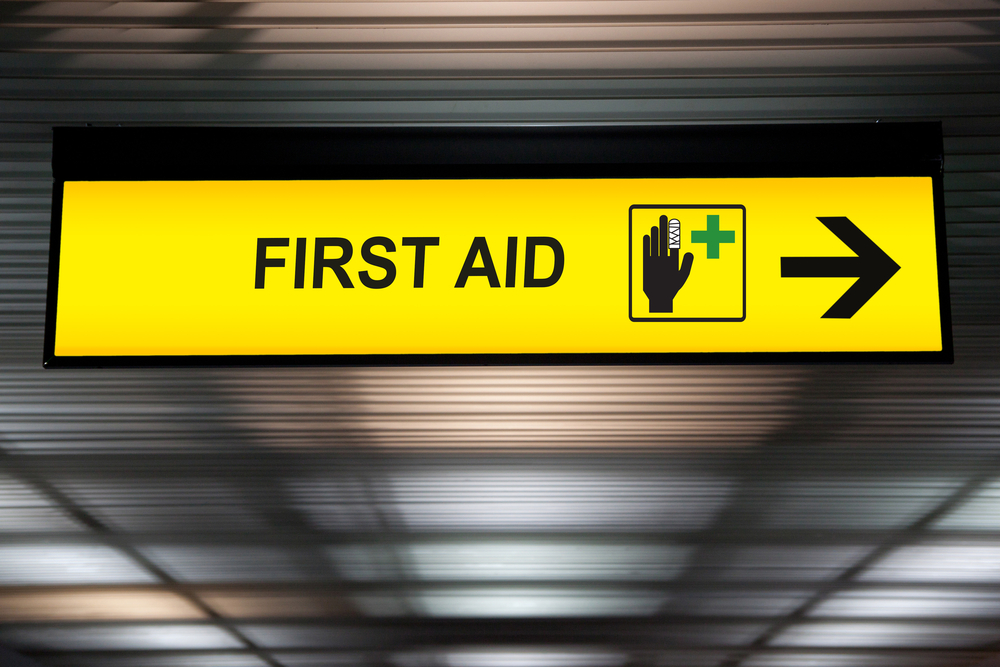
10.) Employee Safety Training and Documentation
Safety is a team effort, and ongoing training is key to keeping everyone informed and prepared. Conduct an annual review of safety training records, ensuring that all employees are up-to-date on required safety courses and certifications. Use this opportunity to schedule refresher courses or address new safety protocols. Annual training doesn’t just tick a compliance box; it empowers employees with the knowledge to work safely and respond effectively to emergencies.
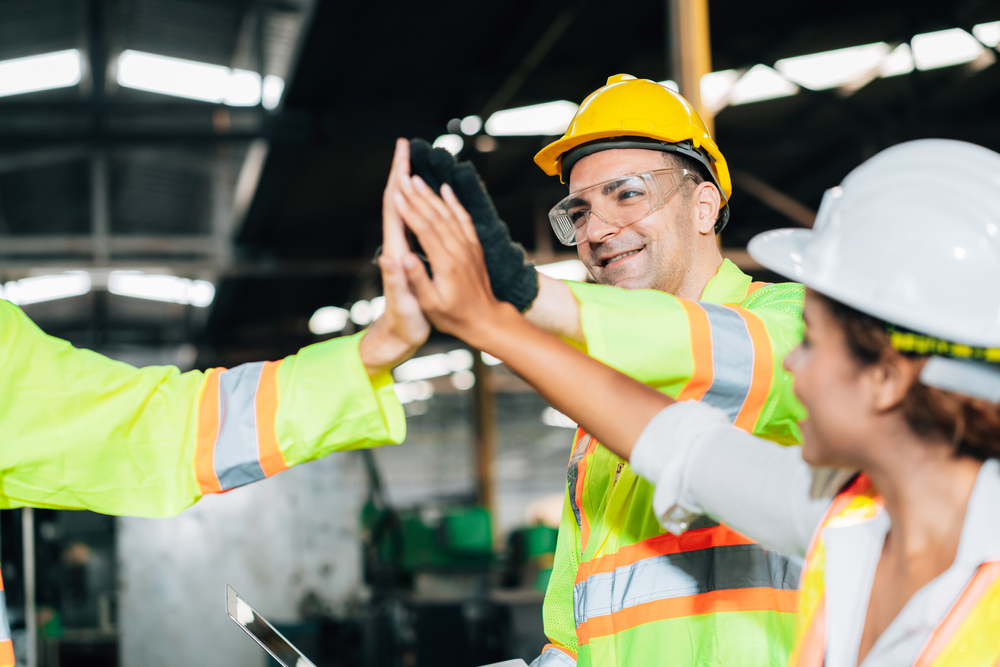
By incorporating these top 10 safety checks into your annual routine, you’re taking tangible steps toward a safer, more compliant facility.
These checks not only enhance operational efficiency but also foster a culture of safety that keeps employees protected and confident in their work environment.
Remember, these checks are just the starting point. As regulations evolve and facility needs change, your safety protocols should adapt as well. A proactive approach to safety means staying informed, updating practices regularly, and always prioritizing the well-being of your team. After all, a safe facility isn’t just compliant; it’s a productive and resilient one.
Ready to get started on this year’s safety check? Begin with this checklist and ensure your facility is on track for a safe, compliant, and successful year ahead.
Do you have a need for our services?
Lewis Bass can help your team identify the most common safety issues in your facility, along with providing immediate referrals to our trusted partners to address them on your behalf.
Not sure what service you need from us?
Take our service identifier quiz here.
Are you uncertain if your equipment is unlisted or not at your facility?
Lewis Bass has you covered here as well: download our unlisted equipment self-identification flyer here.
Do you have a need for an urgent machinery evaluation?
Please reach out to us using our contact form here or call/text us directly on our office line 408-942-8000. We are always available to help with rush jobs and permit-blocking safety situations at your facility.