The Importance of Preventative Maintenance for Safety
If there’s one thing every facility manager, safety officer, or business owner should take seriously, it’s preventative maintenance.
The difference between a well-maintained operation and one riddled with safety hazards often comes down to routine inspections, timely repairs, and adherence to industry standards. Yet, too often, maintenance gets pushed down the priority list—until something goes wrong.
Let’s talk about why preventative maintenance isn’t just a good idea but a crucial investment in long-term safety. And since electrical hazards are among the most dangerous risks in any facility, we’ll also explore how staying compliant with NFPA standards can keep your team safe and your operations running smoothly.
How Preventative Maintenance Improves Workplace Safety
Preventative maintenance is about identifying and addressing issues before they turn into costly failures or safety incidents. By implementing a structured maintenance program, businesses can:
- Reduce the risk of unexpected equipment failures
- Enhance workplace safety by addressing hazards proactively
- Extend the lifespan of critical machinery and infrastructure
- Ensure compliance with safety regulations and industry standards
Neglecting maintenance doesn’t just lead to breakdowns—it puts employees at risk of injury and exposes businesses to regulatory fines, liability issues, and downtime. Let’s break down the key areas where preventative maintenance plays a crucial role in workplace safety.
The Role of Electrical Safety in Preventative Maintenance
Electrical systems are the backbone of most industrial and commercial facilities, but they also pose significant hazards if not properly maintained. Faulty wiring, overloaded circuits, and deteriorating equipment can all lead to fires, electrocution, and system failures.
NFPA Compliance and Electrical Safety
The National Fire Protection Association (NFPA) provides guidelines that help facilities maintain safe electrical systems. Two critical standards to be aware of include:
- NFPA 70 (National Electrical Code) – Outlines installation requirements to minimize electrical hazards.
- NFPA 70B (Recommended Practice for Electrical Equipment Maintenance) – Focuses on best practices for electrical preventative maintenance.
Regular inspections, thermal imaging to detect overheating, and scheduled servicing of electrical panels can significantly reduce the risk of failures and fires. Preventative maintenance under NFPA guidelines ensures that businesses don’t just react to problems but actively prevent them.
Key Electrical Maintenance Tasks
To stay ahead of electrical safety risks, facilities should implement the following maintenance measures:
- Routine Inspections: Check for frayed wires, loose connections, and corrosion.
- Infrared Scanning: Detect overheating components before they fail.
- Breaker Testing: Ensure circuit breakers function correctly to prevent overloads.
- Load Balancing: Prevent overheating and inefficiency in electrical distribution.
- Grounding Checks: Verify that all electrical systems are properly grounded to avoid shocks and fire hazards.
By incorporating these measures into your preventative maintenance program, you not only enhance safety but also reduce the likelihood of unplanned downtime and costly repairs.
Beyond Electrical: Other Critical Maintenance Areas
While electrical safety is paramount, a strong preventative maintenance program should also cover other facility areas, including:
HVAC Systems
Proper maintenance of heating, ventilation, and air conditioning systems improves indoor air quality, prevents mold growth, and reduces fire risks associated with malfunctioning equipment.
Mechanical Equipment
From forklifts to conveyor belts, mechanical failures can lead to serious injuries. Routine lubrication, belt replacements, and safety checks can prevent malfunctions that put workers at risk.
Fire Protection Systems
Fire alarms, sprinklers, and extinguishers need regular testing to ensure they function in an emergency. Compliance with NFPA 25 (Standard for the Inspection, Testing, and Maintenance of Water-Based Fire Protection Systems) is key to effective fire safety.
Final Thoughts: The True Value of Preventative Maintenance
Preventative maintenance isn’t just a checklist—it’s a mindset that prioritizes safety, efficiency, and long-term cost savings. By staying proactive, businesses can avoid the disruptions, liabilities, and dangers that come with neglected maintenance.
When was the last time your facility’s electrical system was inspected? Are your fire protection systems up to code? If you can’t answer with confidence, it might be time to take a closer look at your preventative maintenance strategy.
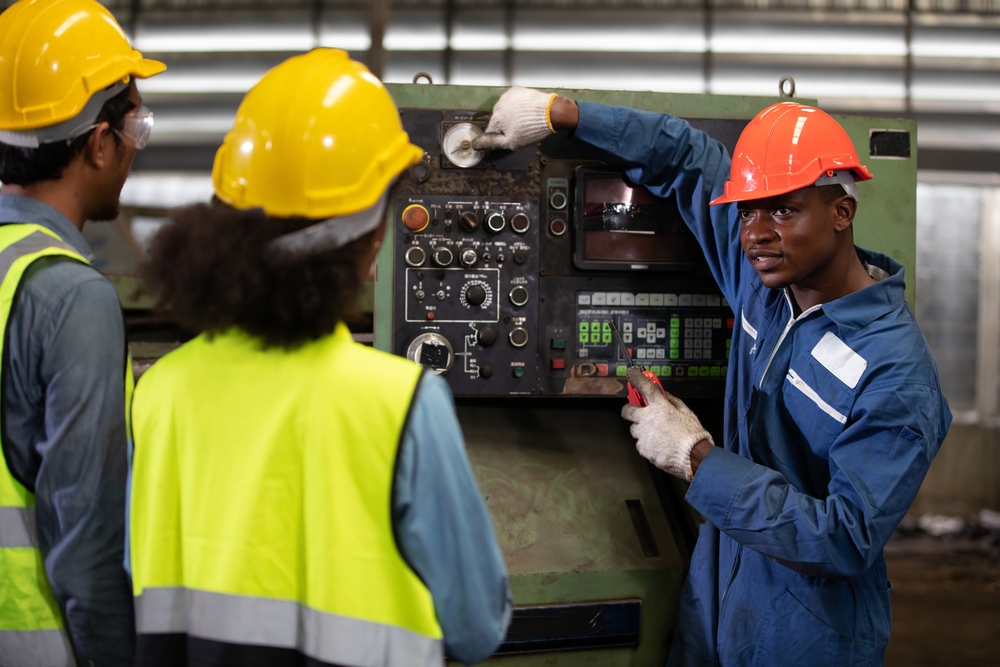
Do you have a need for our services?
Lewis Bass can help your team identify the most common safety issues in your facility, along with providing immediate referrals to our trusted partners to address them on your behalf.
Not sure what service you need from us?
Take our service identifier quiz here.
Are you uncertain if your equipment is unlisted or not at your facility?
Lewis Bass has you covered here as well: download our unlisted equipment self-identification flyer here.
Do you have a need for an urgent machinery evaluation?
Please reach out to us using our contact form here or call/text us directly on our office line 408-942-8000. We are always available to help with rush jobs and permit-blocking safety situations at your facility.