Thermography: A Necessary Facility Maintenance and Inspection Routine
As a facilities manager or safety officer, you know that in order to keep your facilities safe, efficient, and compliant, that there’s a routine list of checks to cover.
But how often does thermography make it on that list? Despite being a lesser-known term to some, thermography is a powerful tool in proactive facility maintenance and inspection. In fact, it might just be the unsung hero your facility needs to prevent costly downtime and ensure a safe environment for employees and visitors alike.
Thermography isn’t just for high-tech industries or facilities with sensitive equipment. Any facility that uses electrical systems, mechanical equipment, or complex HVAC systems can benefit. This week’s blog is all about why thermography should be a routine part of your maintenance and inspection protocols, how it works, and what you can expect from implementing it in your facility.
What is a Thermographic Inspection?
Thermographic Inspections, otherwise referred to generally as “Thermography” is a process that uses infrared (FLIR) cameras to capture temperature variations across surfaces. These infrared scans provide a “heat map” of a given area, showing where potential issues might be lurking. Heat is a telltale indicator of problems – whether it’s an overloaded circuit, a failing bearing, or an unbalanced HVAC system. Hot spots, or areas with unusual heat signatures, often indicate developing issues that can lead to breakdowns or even fire hazards if left unchecked.
Using thermography, facility managers can detect hidden problems long before they become visible or escalate into emergencies. Unlike other inspection methods, thermography is a non-invasive technique. It allows you to get a snapshot of the facility’s health without dismantling equipment or interrupting daily operations. For facilities trying to juggle safety with productivity, thermography offers the best of both worlds.
Why is Thermography Essential for Facility Maintenance?
Now, you might be thinking, “My facility hasn’t had any major issues, so why add another routine?” That’s precisely why thermography is essential: it’s proactive. Here are three core reasons why thermography should be part of every facility maintenance and inspection routine:
- Early Detection of Electrical Issues: Electrical systems are a core part of any facility, and they’re also one of the most common culprits for failures. Electrical hotspots can appear in overloaded circuits, loose connections, or faulty wiring. Without thermography, these issues can go unnoticed until they cause a costly shutdown or, worse, an electrical fire. Regular thermographic scans can catch these issues in their early stages, giving facility managers time to schedule repairs before they escalate.
- Improved Equipment Lifespan: Think of thermography as a “check engine light” for your equipment. As machinery operates, natural wear and tear happen, and some components may start to overheat. When left unchecked, this heat buildup can accelerate wear on equipment, leading to premature failure. By identifying these issues early with thermography, maintenance teams can address them before they shorten the life of critical assets.
- Energy Efficiency Gains: Thermography can also reveal energy inefficiencies. Unbalanced HVAC systems, for instance, often show up as hot or cold spots, indicating areas where energy is being wasted. In a large facility, these inefficiencies add up over time. Addressing them not only reduces energy bills but also helps meet sustainability goals—a win-win.
How Often Should Thermography Be Part of Your Routine?
The frequency of thermographic inspections depends on your facility’s unique risk factors. For facilities with high-power equipment or critical infrastructure, quarterly or semi-annual inspections might be best. For smaller, less complex facilities, an annual thermographic inspection may suffice. As with any maintenance routine, consistency is key. Regular thermographic inspections allow you to track changes over time and spot trends that may indicate emerging risks.
What Does a Thermography Inspection Look Like?
During a thermographic inspection, a technician will use an infrared camera to scan various components within your facility. These might include electrical panels, motors, pumps, HVAC systems, and more. The images produced will display temperature variations, often color-coded to make hot and cool spots easy to identify. A trained thermographer can then analyze these images, flagging any anomalies that may suggest problems.
Typically, thermography inspections are quick and minimally disruptive. Depending on the size and complexity of the facility, inspections can take as little as an hour or extend to a full day for more comprehensive analyses. Once completed, the thermographer provides a detailed report, highlighting potential problem areas and recommended corrective actions.
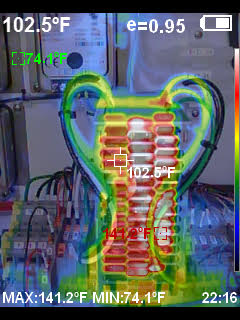
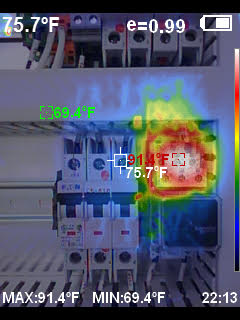
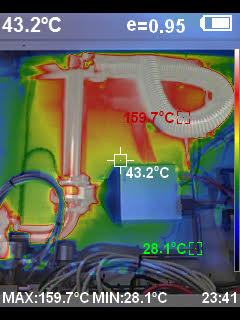
The Insurance Benefits of Thermographic Inspections
What many facility managers don’t realize is that thermographic inspections can play a significant role in reducing insurance premiums and, in some cases, avoiding claims altogether. By identifying potential hazards before they lead to accidents or system failures, thermography demonstrates a proactive approach to risk management that insurers look favorably upon.
For instance, insurance companies often view thermographic inspections as a preventative measure that reduces the likelihood of costly incidents, such as electrical fires or mechanical failures. Facilities that can show a record of routine thermographic inspections may be eligible for discounts on their premiums or even preferred coverage terms. Some insurers will also require thermographic scans for high-risk facilities or critical equipment, making it easier to comply with policy requirements and reduce the chance of denied claims in the event of an incident.
Investing in Thermography: Is It Worth It?
In the world of facility management, budgets are tight, and every expenditure must be justified. While thermography isn’t the cheapest tool in the toolkit, its benefits far outweigh the cost, especially when you consider the expense of unexpected downtime, repairs, or liability. A single thermographic inspection could reveal an issue that, if left unchecked, would cost thousands to repair. It’s a small investment to make for the peace of mind that comes with knowing your facility is running safely and efficiently.
Do you have a need for our services?
Lewis Bass can help your team identify the most common safety issues in your facility, along with providing immediate referrals to our trusted partners to address them on your behalf.
Not sure what service you need from us?
Take our service identifier quiz here.
Are you uncertain if your equipment is unlisted or not at your facility?
Lewis Bass has you covered here as well: download our unlisted equipment self-identification flyer here.
Do you have a need for an urgent machinery evaluation?
Please reach out to us using our contact form here or call/text us directly on our office line 408-942-8000. We are always available to help with rush jobs and permit-blocking safety situations at your facility.