Machine Nameplates: The A-Z of NFPA 79 Requirements
The History and Components of a Nameplate
Machine nameplates have a history dating back to their first use by St. Paul’s Stamp Works, which issued their first identification nameplate to a local company in the mid 1920s.
Much has changed since then. Nameplates are now a requirement for all consumer, industrial, medical, and high tech machinery worldwide. In the United States, the NFPA has issued formal nameplate content standards and new updates to nameplate requirements throughout the years.
What Information is Required on a Nameplate?
Nameplate information shall* include:
*The usage of shall in this case with regards to nameplate requirements per NFPA 79 means it is mandatory inclusion, not optional as should could imply.
- Manufacturer and serial number (model optional)
- Voltage, frequency, and phases
- Overcurrent protection size (Circuit breaker)
- SCCR (short circuit current rating)
- Full load and largest load current
- Electrical schematic number
1. The full-load current shown on the nameplate shall not be less than the full-load currents for all motors and other equipment that can be in operation at the same time under normal conditions of use. Where unusual loads or duty cycles require oversized conductors, the required capacity shall be included in the full-load current specified on the nameplate |
2. Nameplate must be plainly visible. |
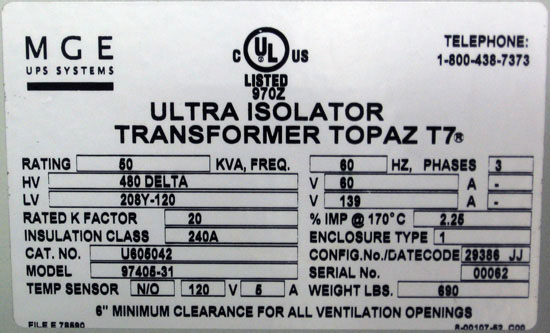
A typical machine nameplate for a transformer.
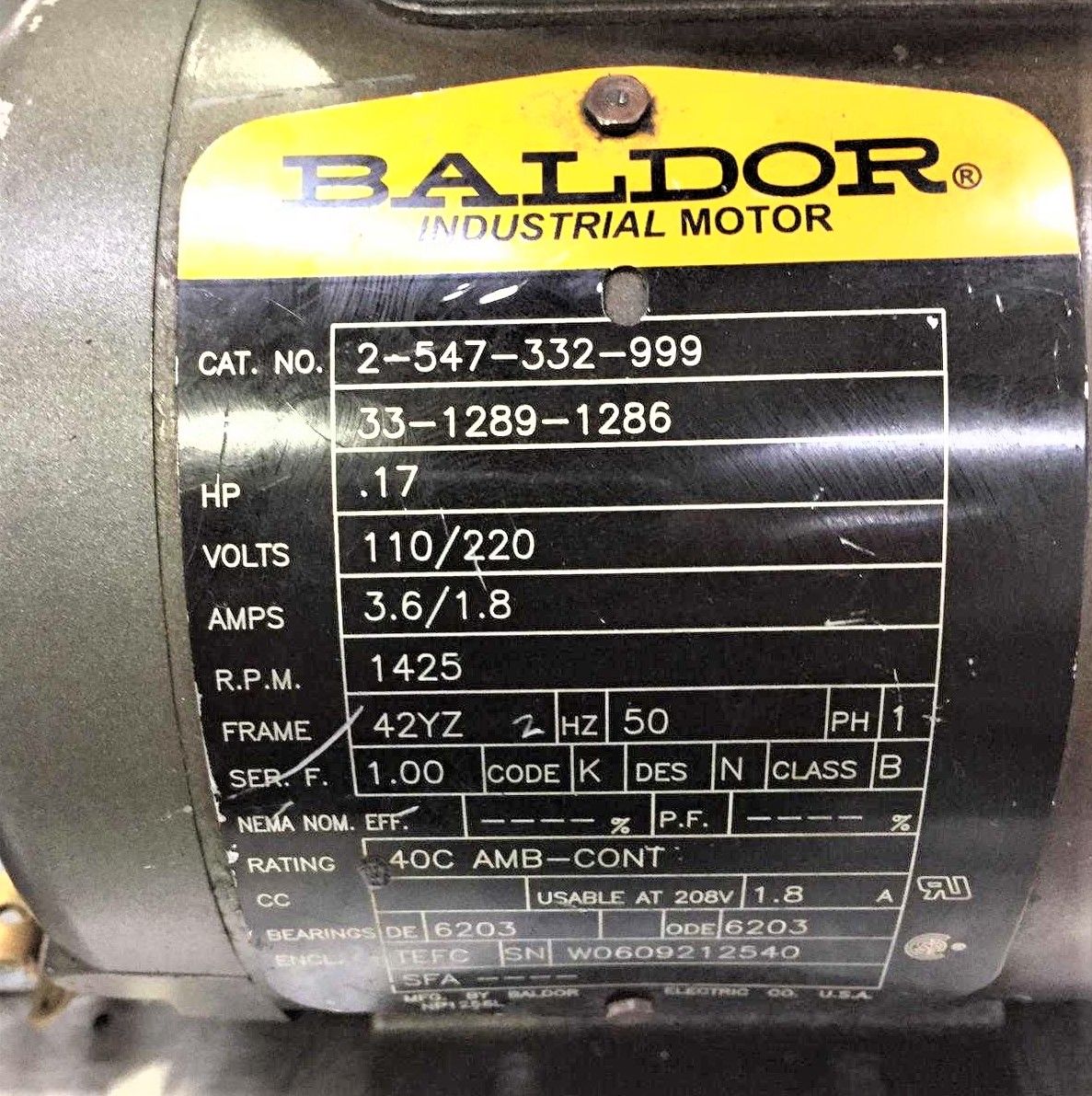
A common example of an older electric motor nameplate.
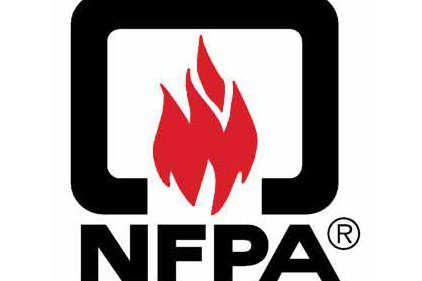
Machine Nameplate Requirements According to NFPA 79
NFPA 79’s Chapter 16 Marking and Safety Signs section has clear guidance on the expectations and components required of a machine nameplate in North America, those of which include the following:
16.4 Machine Nameplate Data.
16.4.1 Control equipment shall be legibly and durably marked in a way that is plainly visible after the equipment is installed. A nameplate giving the following information shall be attached to the outside of the enclosure, or on the machine immediately adjacent to the enclosure: (1) Name or trademark of supplier (2) Model, serial number, or other designation (3)*Rated voltage, number of phases and frequency (if ac), and full-load current for each supply (4) Ampere rating of the largest motor or load (5) Maximum ampere rating of the short-circuit and groundfault protective device, where provided (6) Short-circuit current rating of the industrial control panel (7) Electrical diagram number(s) or the number of the index to the electrical drawings
16.4.2 The full-load current shown on the nameplate shall not be less than the full-load currents for all motors and other equipment that can be in operation at the same time under normal conditions of use. Where unusual loads or duty cycles require oversized conductors, the required capacity shall be included in the full-load current specified on the nameplate.
16.4.3 Where more than one incoming supply circuit is to be provided, the nameplate shall state the information in 16.4.1 for each circuit.
16.4.4 Where only a single motor or motor controller is used, the motor nameplate shall be permitted to serve as the electrical equipment nameplate where it is plainly visible.
16.4.5 Where supply conductor and machine overcurrent protection is furnished as part of the machine, the machine shall be marked “Supply conductor and machine overcurrent protection provided at machine supply terminals.” A separate nameplate shall be permitted to be used for this purpose
Nameplate SCCR Requirements
As mentioned in our blog Short Circuit Current Rating (SCCR) and Your Industrial Equipment , SCCR is a required nameplate item since the release of the 2005 NEC.
The short-circuit current rating (SCCR) is important to know when designing and installing an electrical control panel because of its role in over-current protection.
The SCCR is the maximum current (in amps) that an electrical device or control panel is able to withstand for three (3) VAC electrical cycles, or during the operation of an over-current protection device such as a fuse.
UL 508A, the standard for industrial control panels in the United States, provides the below instructions for determining the SCCR of a control panel:
1. Determine the SCCR of all individual power components and UL approved series ratings.
a. Examine all individual components and record their SCCRs.
b. If SCCR is not marked or known, use UL508A default Table SB4.1
c. Check and record any UL approved series ratings.
d. Note the minimum SCCR in the feeder circuit and each branch circuit.
2. Modify the SCCR of certain series combinations and record their SCCRs.
a. If current limiting fuses are used in the feeder circuit, compare the Ipeak of the fuse from UL 508A Table SB4.2 to the lowest rated SCCR component or minimum SCCR in each branch circuit.
b. The Ipeak of the fuse must be less than or equal to the lowest rated SCCR of any component or SCCR in each branch circuit.
3. The SCCR of the panel is equal to the lowest rated SCCR of any:
a Overcurrent protective device
b. UL approved series SCCR rating
c. Modified combinations from Step 2
d. Power component not affected by Step 2
Source: http://www.littelfuse.com/data/en/Training_Module/LittelfuseSCCRPresentationAug20061.pdf
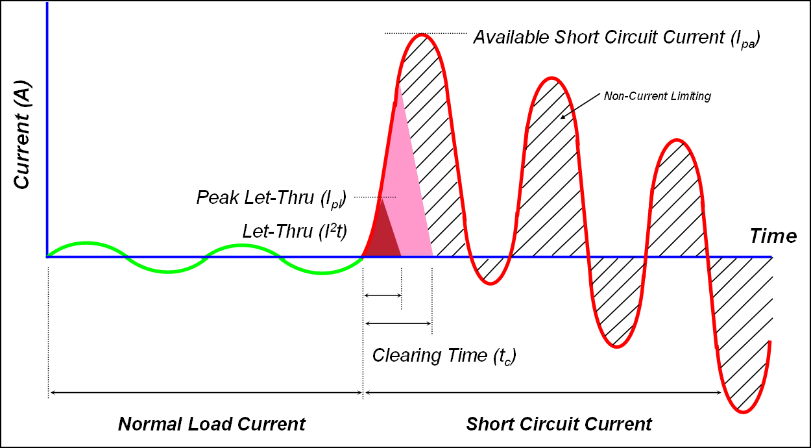
Image Source: https://www.revereelectric.com/roller/UnilogBlog/entry/ul-508-and-nec-code
Nameplate Material and Durability
When it comes to machine nameplates, what’s written is only half the story. While NFPA 79 requires the nameplate to be “permanent and legible,” it leaves the details of material selection and environmental durability up to the manufacturer or equipment evaluator.
Choosing the Right Nameplate Material
Here’s a quick breakdown of commonly used materials and how they hold up in the field:
Material | Pros | Cons |
---|---|---|
Anodized Aluminum | Lightweight, corrosion-resistant, affordable | Can fade under extreme UV if untreated |
Stainless Steel | Excellent chemical and heat resistance | More expensive, heavier |
Polycarbonate/Plastic Laminate | Cost-effective, customizable | Less durable in high-heat or abrasive environments |
Polyester (Mylar) | Flexible, resistant to many solvents | Not ideal for rugged industrial use |
And For Those of Us Who Like Charts
Here is a chart showing a comparison between different types of materials nameplates can be manufactured from and the environments they are best suited for use in:
Environmental Considerations
When selecting or evaluating nameplates, think beyond the shop floor:
-
High-humidity environments (like food processing) call for corrosion-resistant materials such as stainless steel or sealed anodized plates.
-
Outdoor equipment should prioritize UV resistance and weatherproof adhesives or mechanical fastening.
-
Heavy industrial zones with vibration and abrasion may benefit from engraved or etched metal plates bolted directly to the enclosure.
Legibility That Lasts
Even if your nameplate meets today’s requirements, will it still be legible five years from now?
✅ Use high-contrast text
✅ Consider laser-etching or embossing for permanence
✅ Avoid ink-based prints unless fully UV-stable and protected
Bottom line? A durable nameplate is more than a compliance checkbox—it’s a critical component of your long-term safety and inspection strategy.
Nameplates and Inspection Requirements
When considering a third party electrical evaluation for a machine in your facility, it is important to ensure that nameplate is both visible and legible to a visiting inspector.
As listed above, the NFPA has an actual code addressing this exact scenario in section 16.4 entitled ‘Machine Nameplate Data’.
Let’s look into what this exact code specifies regarding visibility:
16.4.1 Control equipment shall be legibly and durably marked in a way that is plainly visible after the equipment is installed.
When seeking an inspection for your equipment that may not have a nameplate or an incomplete nameplate, a Lewis Bass engineer will request as much documentation and identifying materials as possible to establish a baseline for the machine to be tested against.
Once enough material has been collected to begin a formal electrical evaluation of the equipment, the machine operator will be expected to produce an accurate nameplate for future inspectors to take note of if the unlisted machinery happens to be moved or involved in an accident in the future.
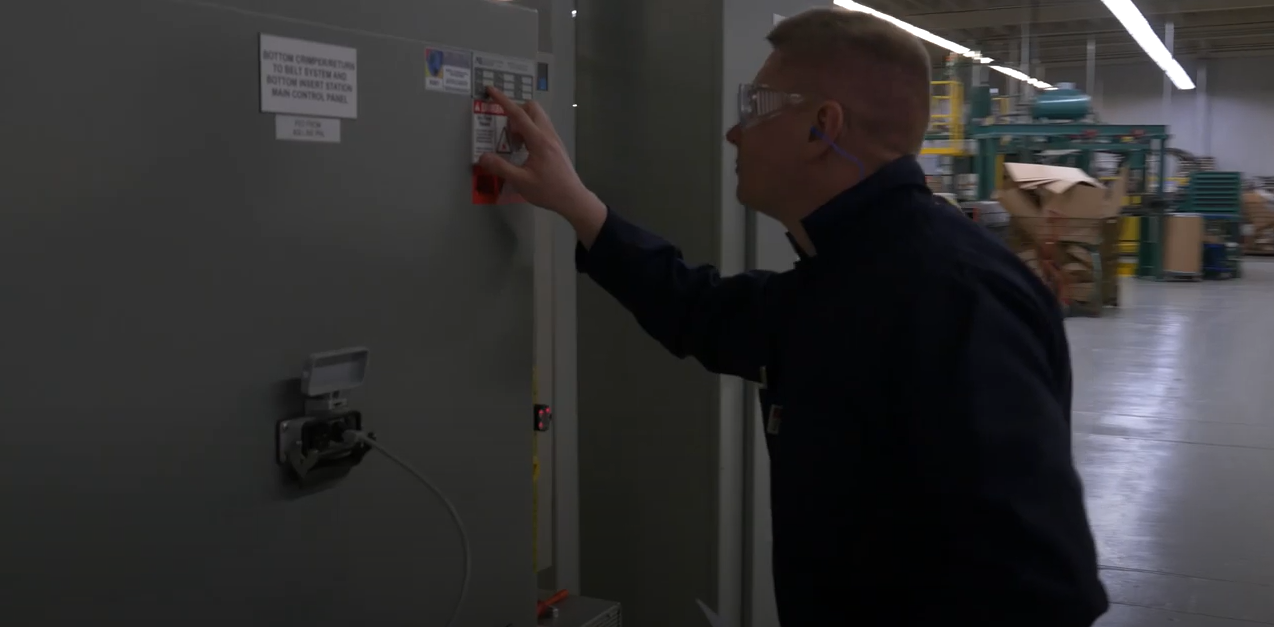
A Lewis Bass Engineer Verifying Nameplate Data
Digital Asset Traceability and QR Codes: Bringing Your Nameplates Into the 21st Century
When Lewis Bass redesigned its Field Evaluation Labels in 2020, management decided to offer our clients the ability to access reports per each unique QR code that we had added to our redesigned label. This meant that our clients could always request a copy of the field report for providing it to the city or to a future buyer of the equipment, should it be sold second-hand.
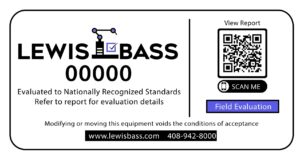
But what about you, the manufacturer or you, the person/company buying a piece of equipment from that manufacturer? What value does a QR code or other embedded tracking system added to a nameplate (which becomes more like a digital nameplate) provide in this instance?
What Is a Digital Machine Nameplate?
A digital nameplate includes a scannable code (usually a QR code) that links to dynamic, cloud-hosted documentation.
This accessible documentation could include any of the below key documents associated per each unique machine:
-
The machine’s full operation manual
-
Lockout/Tagout (LOTO) procedures
-
Electrical schematics and panel layouts
-
Inspection or repair history
-
Contact information for service or support
QR Code Integration: Practical Guidelines
If you’re considering this feature, keep these NFPA 79-compatible tips in mind:
-
Placement matters: Ensure QR codes are near (but not replacing) the physical nameplate info
-
Code durability: Use etched or printed UV-resistant QR codes with permanent adhesives or mechanical backing
-
Minimum size: Aim for at least 0.75 in x 0.75 in for readability with gloves and in low light
-
Offline fallback: Ensure the critical information is still accessible in case of connectivity loss
The ROI of Smarter Nameplates
Adding digital traceability to your nameplate system can:
-
Reduce troubleshooting time
-
Enable faster AHJ inspections by linking directly to compliance documentation
-
Support preventative maintenance schedules and audits
-
Improve equipment lifecycle management
A digital nameplate is the future of machine compliance that aligns with both Industry 4.0 trends and field evaluation best practices.
Download the Lewis Bass NFPA 79 Nameplate Checklist
Here at Lewis Bass we work with many clients that have had issues with nameplates on their equipment either missing important (and required) data and/or having nameplates designed that are not suitable for the environment their equipment is to be installed in. If you’d like an easy-to-follow checklist that goes over the best practices of nameplate design for meeting NFPA 79 compliance and beyond, please click this link here to download this handy PDF checklist.
Do You Need an Evaluation of Equipment at Your Facility?
Are you in need of an electrical evaluation for known or potentially unlisted equipment in your facility that may or may not have complete machine nameplates visible?
If so, please reach out to Lewis Bass International Engineering Services today for an expedited quote for 3rd party field label, SEMI S2/S8, or CE Marking services.