Would you prefer an IRS audit or a OSHA safety inspection?
Few things in life are scarier than an IRS audit.
But, if you or your team also happen to be operating industrial machinery without the proper paperwork and third party field labels/UL labels on them, you may find yourself subject to an OSHA safety inspection.
Anytime the government shows up at your door you will have a problem.
But, which one is worse from a financial point of view?
The answer may surprise you.
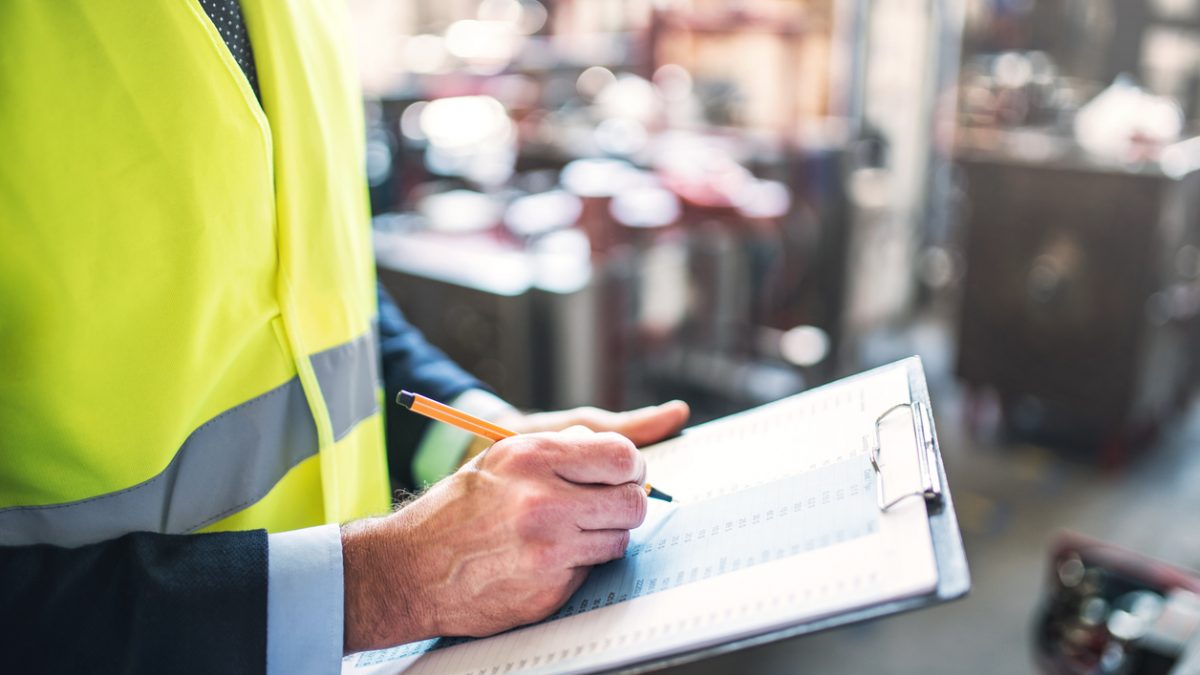
An IRS Audit can be stressful and time consuming.
This is due to the sheer amount of documentation required to establish whether or not clerical mistakes or criminal motives are at play in the discrepancies found.
IRS Audits are almost never resolved in one day. From the time you receive an audit notice – to final resolution, including any appeal – can take up to 2 years.*
Most of your time spent will be on gathering accurate records and data going as far as 6 years back.
Typical IRS Audit requests include:
- Receipts
- Bills
- Canceled checks
- Legal papers
- Loan agreement
- Logs or diaries
- Tickets
- Medical and Dental records
- Theft or loss documents, and more.
While the time spent in preparing for the audit is a major ordeal and counts on your business keeping excellent records of all possible transaction types, contracts, and agreements; the tax due and the penalties you’ll pay are easily calculable and will end when the Audit ends.
But, what if the Audit never ended?
*Source: https://www.irsmind.com/audits/how-long-does-it-take-to-resolve-a-tax-audit/
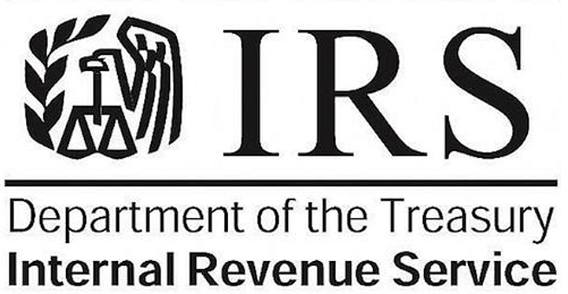
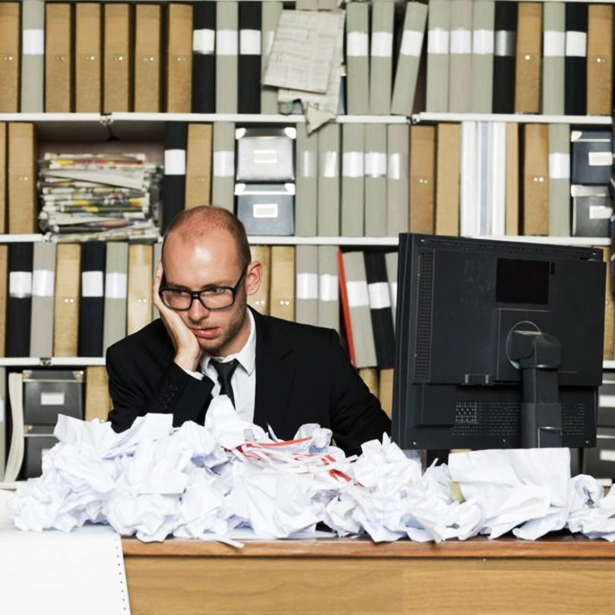
A OSHA Safety Inspection is like an endless corporate safety audit.
In addition to being significantly longer compared to an IRS Audit, OSHA Safety Inspections require continued oversight and surprise inspections to verify that your facility and equipment are safe to use and to also confirm that their required safety fixes have been enacted for machinery and that your OSHA-approved safety processes and procedures are being enforced in your facility.
Financial penalties are not a simple matter for OSHA Safety Inspections. While an IRS Audit has known fixed costs of tax due and variable penalties and interest, OSHA penalties are the same per-machine and per facility safety-violation and can be enforced at $13,653.00 each. In addition, if you willfully violated the abatement period set with OSHA to become compliant, the fines then start at $13,653.00/day for your facility.
If you were to continue to willfully violate OSHA’s requirements to allow a third party to electrically evaluate and sticker your facility’s unlisted machinery, keep your facility safe to access, and protect your employees safety when operating machinery and tools, fines then rise to $136,532.00 per violation.
For example, if you had 10 unlisted machines in full production that you refused to evaluate for third party field labels by an FEB like Lewis Bass or an NRTL lab, per OSHA’s instructions, your total fine would be 10 x $136,532.00 = $1,365,532.00. That is a lot of money to pay in fines for just 10 unlisted machines.
Now, what would you prefer—an IRS Audit or a OSHA Safety Inspection?
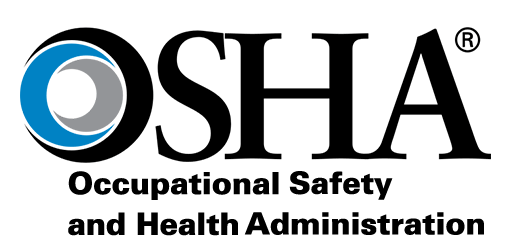
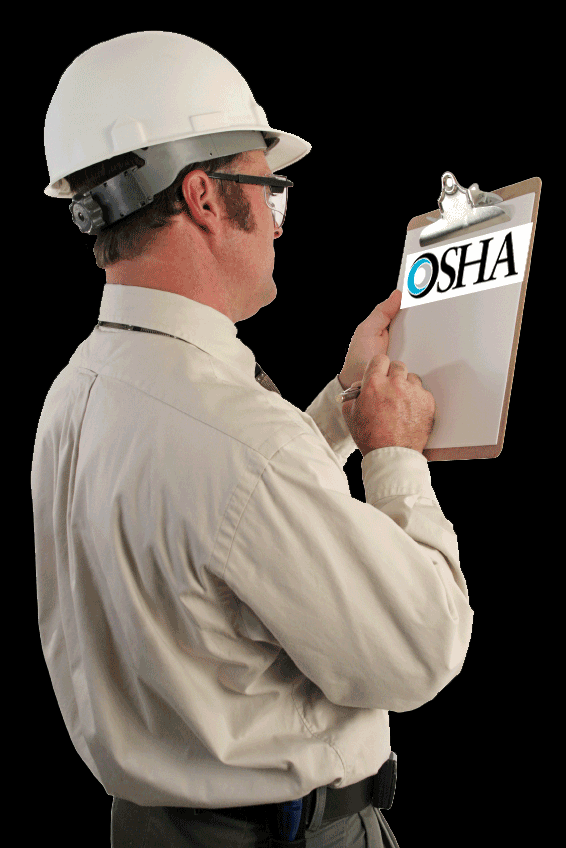
What triggers an OSHA Safety Inspection?
- Investigation of imminent dangers: Any conditions or practices that could reasonably be expected to cause death or serious physical harm to employees immediately or before enforcement action could be taken (these investigations are conducted within 24 hours).
- Fatality and catastrophe investigations: Any work-related incident that results in the death of an employee or the in-patient hospitalization of three or more employees (such incidents must be reported to the nearest OSHA office by telephone or in person within eight hours of the incident).
- Investigations of complaints: For example, complaints made by employees, and referrals.
- Programmed inspections: Regularly scheduled inspections in “high hazard” industries.
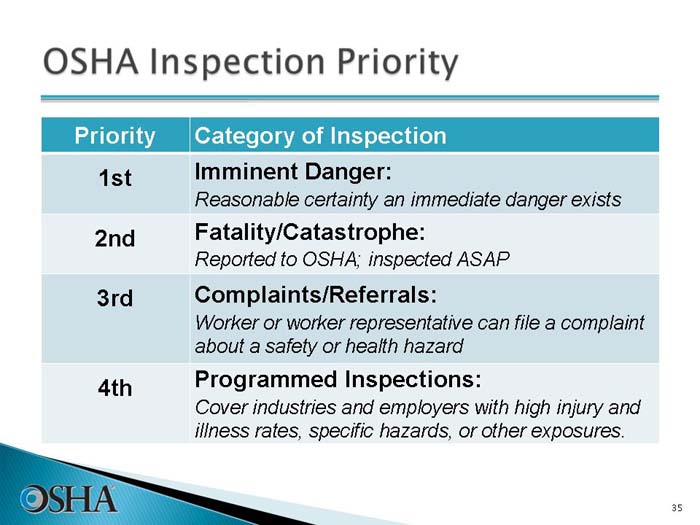
Do you want help avoiding a potential OSHA Safety Inspection at your facility?
Lewis Bass can help get your unlisted equipment evaluated and labeled for legal use and can even help you and your team to identify the most common safety issues in your facility, along with providing immediate referrals to our trusted partners to address them on your behalf.
Not sure what service you need from us?
Take our service identifier quiz here.
Are you uncertain if your equipment is unlisted or not at your facility?
Lewis Bass has you covered here as well: download our unlisted equipment self-identification flyer here.
Do you have a need for an urgent machinery evaluation?
Please reach out to us using our contact form here or call us directly at our office line 408-942-8000. We are always available to help with rush jobs and permit-blocking safety situations at your facility.